在高聚物加工中,超过50%的热塑性塑料是通过挤出加工制造的。挤出过程中,聚合物在挤出机内部经历输送、熔融,以及与助剂或添加物的混合和分散,涉及温度、压力、速度和停留时间分布(RTD)等多个参数。这些参数对挤出效率和最终制品质量有着重要影响。
挤出加工中面临的挑战
在实际生产中,这些问题往往难以通过定量研究解决,工艺调整多依赖于经验,导致需要进行耗时费力的试验,延长了生产周期并造成了原材料的浪费。尤其是在不同材料和配方的工艺切换中,往往需要重新调试工艺条件,这进一步增加了时间成本。
对于使用小规格或低产量设备(如直径75mm、95mm或更小的挤出机,产量数百kg/h)的场景,进行此类试验或工艺调整,材料和成本的消耗尚在可控范围内。但对于大规格设备,调试工艺参数造成的浪费则显得惊人,消耗的时间也让人无法接受。
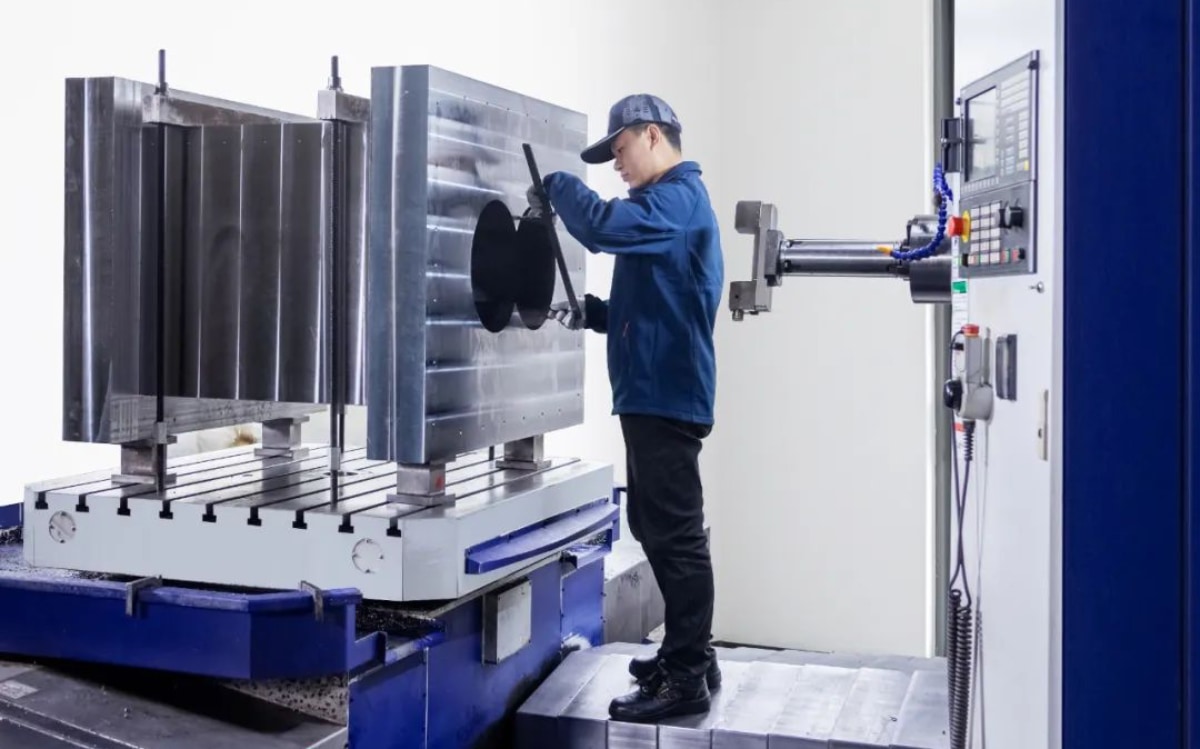
如何解决
因此,采用计算机辅助过程分析和仿真技术来模拟和研究挤出及成型过程已成为更优选择。通过CAE技术,能够优化挤出机的系统设计,降低实验成本,帮助设计和研发人员改善设备及工艺参数,从而提高研发和生产效率,最终获得高质量且具竞争力的产品。
塑料挤出和成型的模拟技术基于流变学和热力学理论,建立聚合物在挤出机和模具内熔融及流动的数学模型,预测和改善产品质量。虽然国外已有多个CAE软件(如Scientific Process & Research的Extruder-PC,Polymer Processing Institute的PASS等)在这方面取得了一定的进展,但挤出类仿真软件的应用仍然不如注射成型CAE软件(如Mold-Flow)普及,主要由于挤出成型的专业性、分类更细以及材料多样性。
取得的成果
近年来,江苏越升科技在大型挤压机和双螺杆挤出机直接挤出等领域取得了显著进展,设备设计和工艺参数探索对挤出成型过程分析和仿真技术的需求日益增加。以单螺杆挤出为基础建立的数学模型已无法满足市场的要求。
江苏越升陈志强董事长在此领域进行了大量探索,开发了具有自主知识产权的聚合物流变和挤出成型过程分析和仿真软件,取得了一系列重要成果。
越升的仿真软件采用了面向对象的分析与设计技术,针对高聚物挤出和成型过程,基于高分子物理学、流变学和热力学等理论,扩展了传统的螺杆三段理论(加料段、熔融段、计量段),深入研究了平行同向双螺杆可采用的各类型和规格型号的螺杆元件,尝试建立了多个相应的数学模型,并编制为不同的函数模块。
在数据库方面,除了常规的标准牌号树脂和无机物数据,越升还增加了数百种热塑性塑料、弹性体、部分橡胶、填料和液体助剂等材料数据。同时,基于公司多年来积累的千余套实验工艺记录对比优化,通过将已知的工艺参数、物料参数和设备参数,包含螺杆组合等作为输入入口变量,探索物料性质、挤出机操作工艺、设备参数与工艺参数之间的关系,从而优化工艺、降低功率消耗,获得更好的制品质量。
自2010年起,越升不断迭代升级仿真软件,目前已更新至2023版。近年来,在大型挤压造粒设备开发设计中,该软件被广泛应用于辅助设计,节约了大量的时间,取得了良好的使用效果。
今年上半年,越升与国内知名客户合作,将该仿真软件应用于超高分子量聚乙烯(UHMWPE)的薄膜挤出成型研究,成功仿真了直径150mm、长径比L/D=72的双螺杆挤出机的实际工况,获得了吻合度良好的工艺数据,同时也对现场运行的越升SAT150的工艺参数调整提供了有效的指导建议,目前设备运行状况良好。
同时,越升的CAE软件还针对客户的物料和配方,探索了不同分子量和配比的工艺条件下的挤出成型参数,为客户节约了大量调试时间,并为后续采用更大规格的挤出机扩大产能奠定了良好基础。
未来展望
塑料挤出行业的进步将推动CAE技术的广泛应用,提高生产效率和产品质量。随着工业4.0的发展,挤出设备将更加智能化,实现实时优化生产过程。新材料的出现为挤出成型带来了新的挑战,江苏越升科技凭借在研发领域的投入及优势,将继续保持领先地位。
与此同时,环保要求促使行业向可持续方向发展,企业将更加注重材料回收和节能减排。随着市场对个性化产品需求的增加,挤出成型技术将变得更加灵活,以快速响应客户需求。